The Story Behind Lyman Products

Anyone who owns more than one firearm probably owns a few Lyman tools. As one of those people, I was excited to get the opportunity to tour Lyman’s 100,000 square foot factory in Middletown, Connecticut.
The company, which employs 120 people at three locations, supplies products for all types of firearms uses. They offered me the opportunity to tour the Middletown facility, and I jumped at the chance.
The Beginning
Lyman was founded in 1878, when William Lyman designed, made and began selling the No. 1 Tang Sight. Its first acquisition came a few years later, when it bought Ideal Reloading Products.
Staying true to its roots, Lyman manufacturers reloading presses, dies, scales and they still make molds for those who wish to cast their own lead bullets. Lyman produces just about every tool a reloader will need as well as punches and other gunsmithing tools. The company also manufactures and sells Tacstar shotgun accessories, Trius Traps and Butch’s firearms cleaning products.
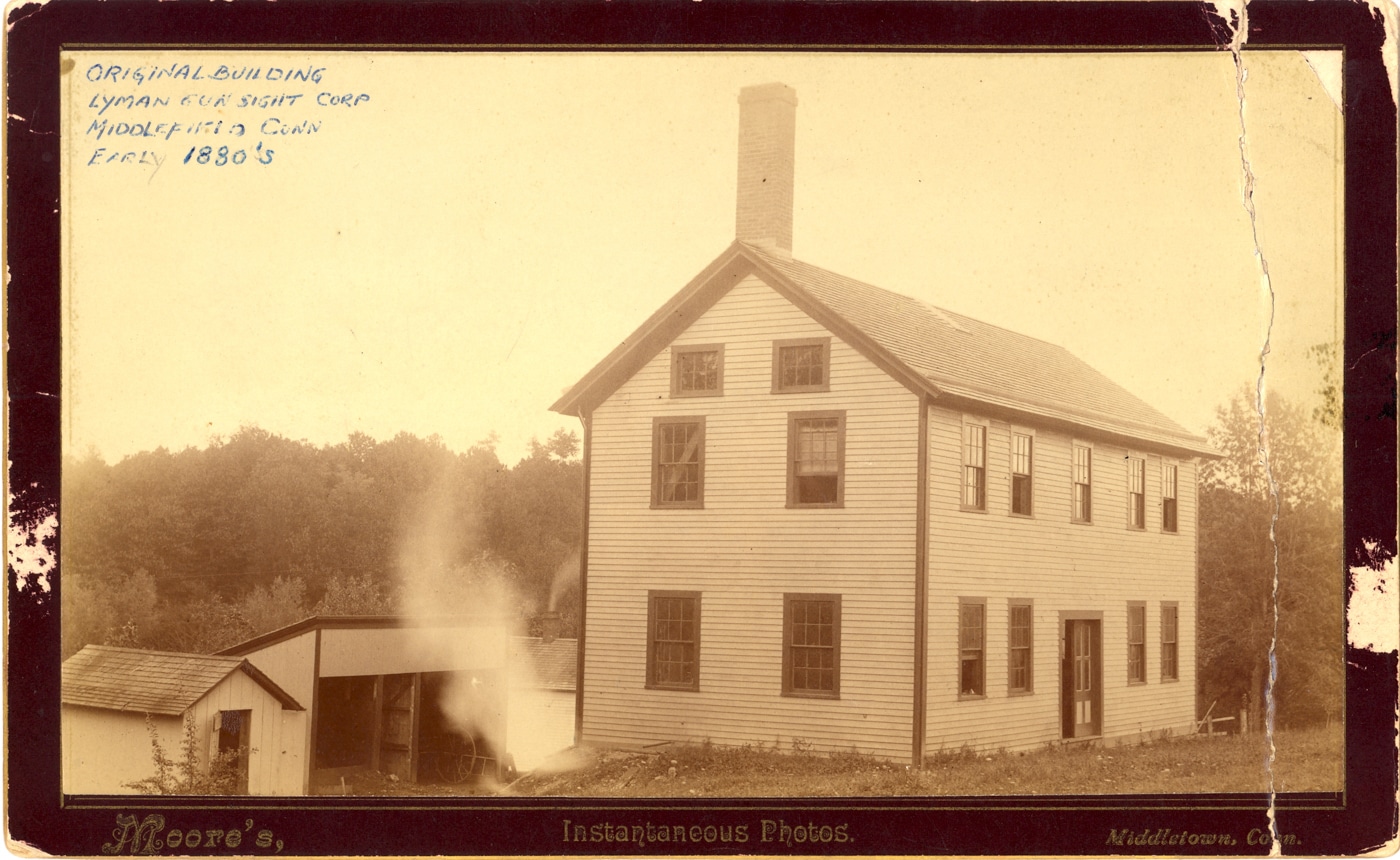
Lyman publishes several, highly specific reloading manuals such as the Long Range Precision Rifle Reloading Handbook, The AR Reloading Handbook, the Lyman Pistol & Revolver Handbook as well as the Shotshell Reloading Handbook. The flagship publication, the Lyman Reloading Handbook, is in its 51st Edition.
While Lyman still makes the “Tang” (or receiver sight) in Middletown, there is much more to Lyman than just reloading and gun sights. Lyman’s success over the past nearly 150 years has been a blend of innovation and acquiring other successful companies within the firearms industry.
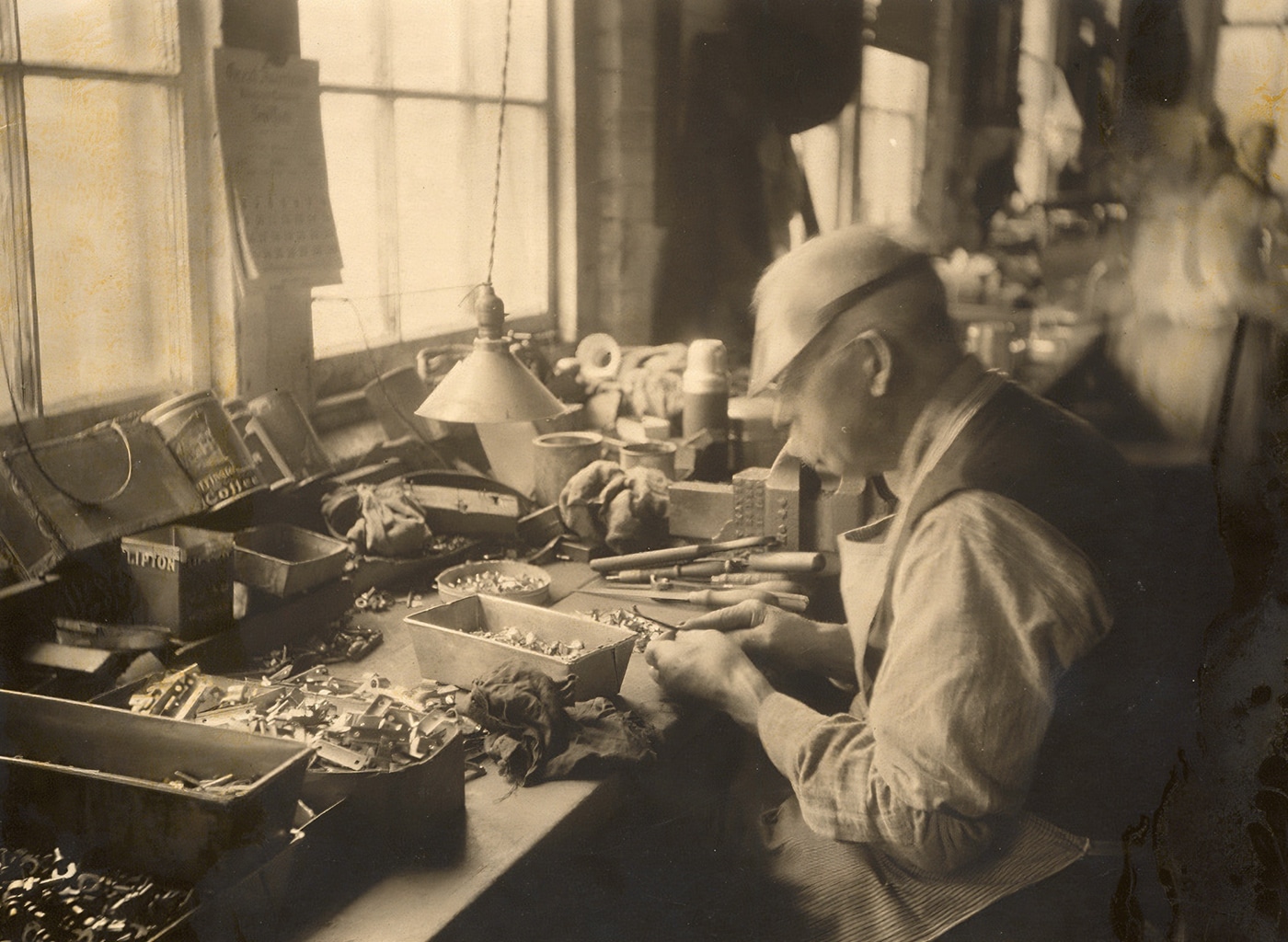
Lyman engineers invented many famous and influential products, and two of the most ubiquitous are as follows: Carbide dies for straight wall pistol cases, and the vibratory tumbler for cleaning brass cartridge cases. Both of these innovations are now taken for granted, but were revolutionary at their launch.
Lyman’s products are carried by all major distributors in the shooting sports industry and sold by both “brick and mortar” and online retailers.
In Practice
I have used many Lyman products for close to 30 years. Why? The high quality and affordability of these American made products has always impressed me. On my factory tour and visit, I wanted to learn more about their processes and as much about their success as company officials were willing to share.
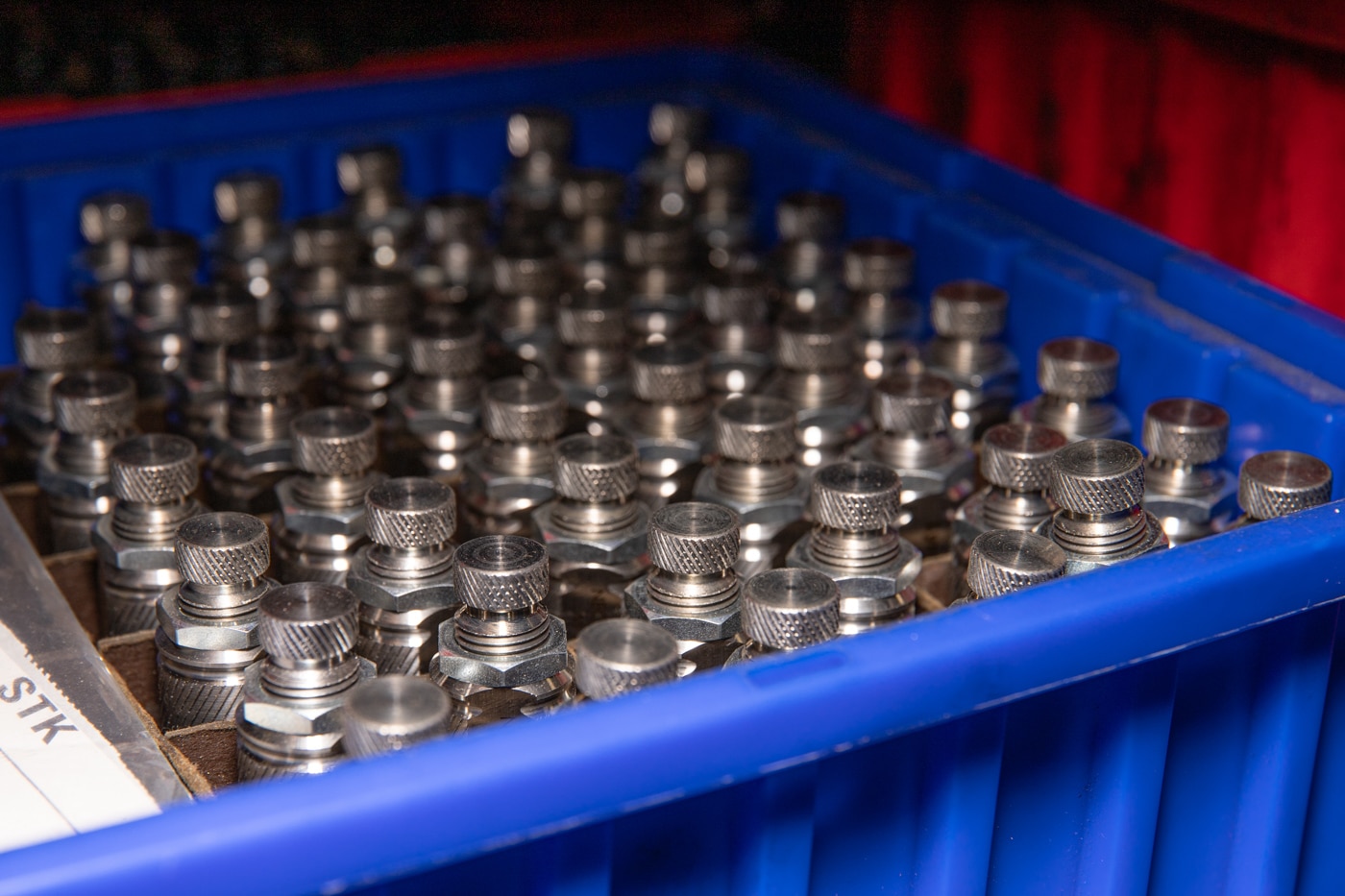
I met with Elizabeth Friedman, the Marketing Services Manager and Tom Griffin, the Ballistic Lab Manager and unofficial company historian. Having worked for the company for more than four decades, Tom probably knows more than anyone about Lyman, its processes and history.
More than 20 years ago, Lyman purchased A-Zoom Snap Caps and brought the manufacturing “in house”. Lyman engineers invented a proprietary, automated process to press the rubber primer into the head of the snap cap. The actual snap caps, which are aluminum, are Computer Numerical Control (CNC) machined, which saves labor and keeps the product affordable.
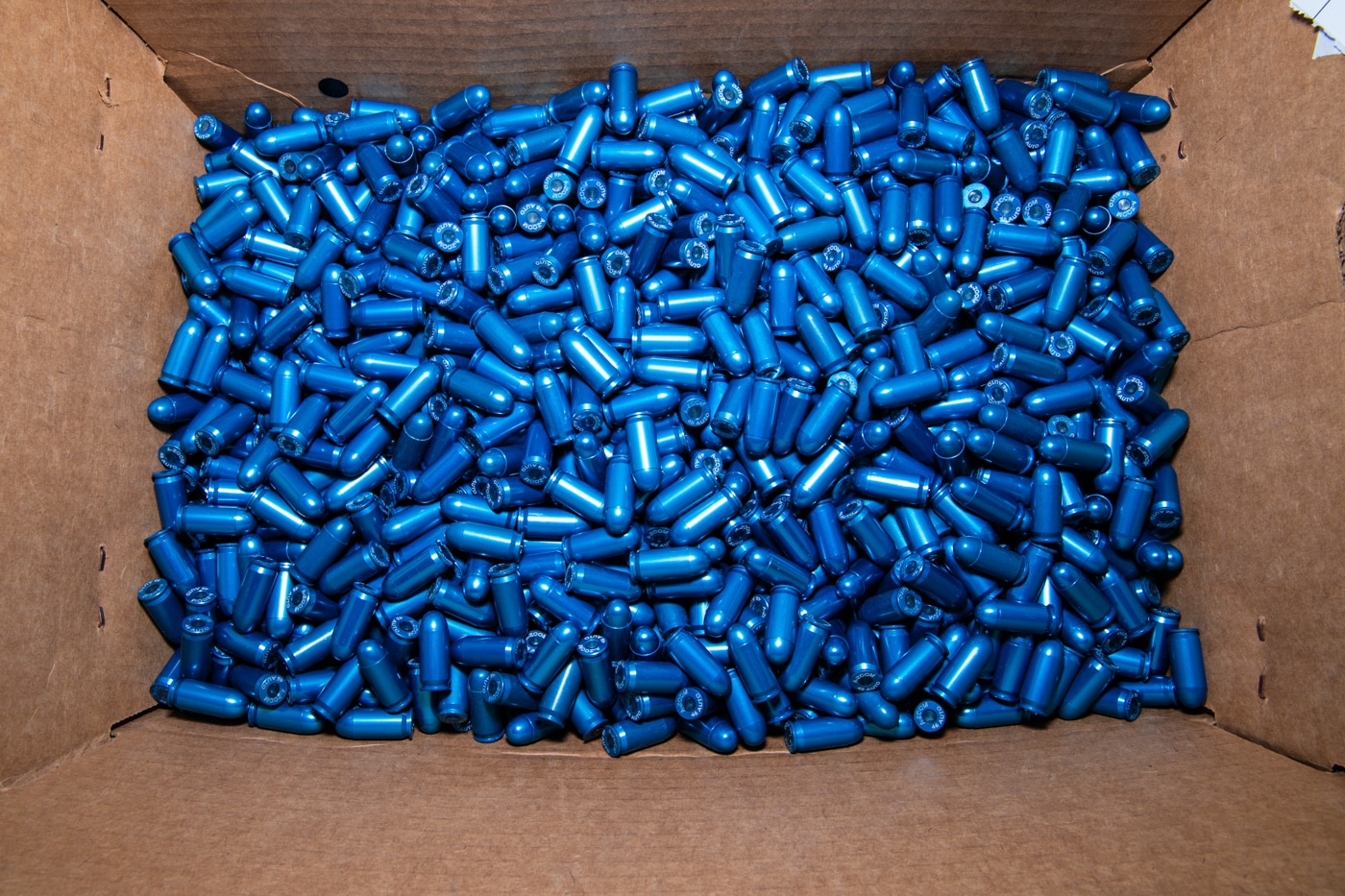
Automation was evident throughout the factory where 22 CNC machines were all working on making everything from snap caps and reloading dies, to doing the finishing machining on reloading press castings. Once a part is secured into one of these modern machines, several operations can be completed. This saves time and costs.
The castings, which will become press frames, are powder coated before machining. This saves costs and time: the machined surfaces do not need to be masked before the powder coat is applied.
I was shown a Coordinated Measuring Machine (CMM), a very precise device that is used to ensure that reloading press frames, which are machined from castings, are within specification. The first piece of each production run is checked and then every fifth piece is checked. If anything is out of specification, production is stopped and workers find out why and fix the problem. The workers running the CMM take their work and quality control very seriously.
The Breadth
To put things in perspective, Lyman catalogs 1,400 different finished goods that include 7,700 different components. The Middletown factory produces 70% of those products. The rest come from sub-contractors or other Lyman facilities. Pachmayr grips, recoil pads and speedloaders are made in an Arizona factory.
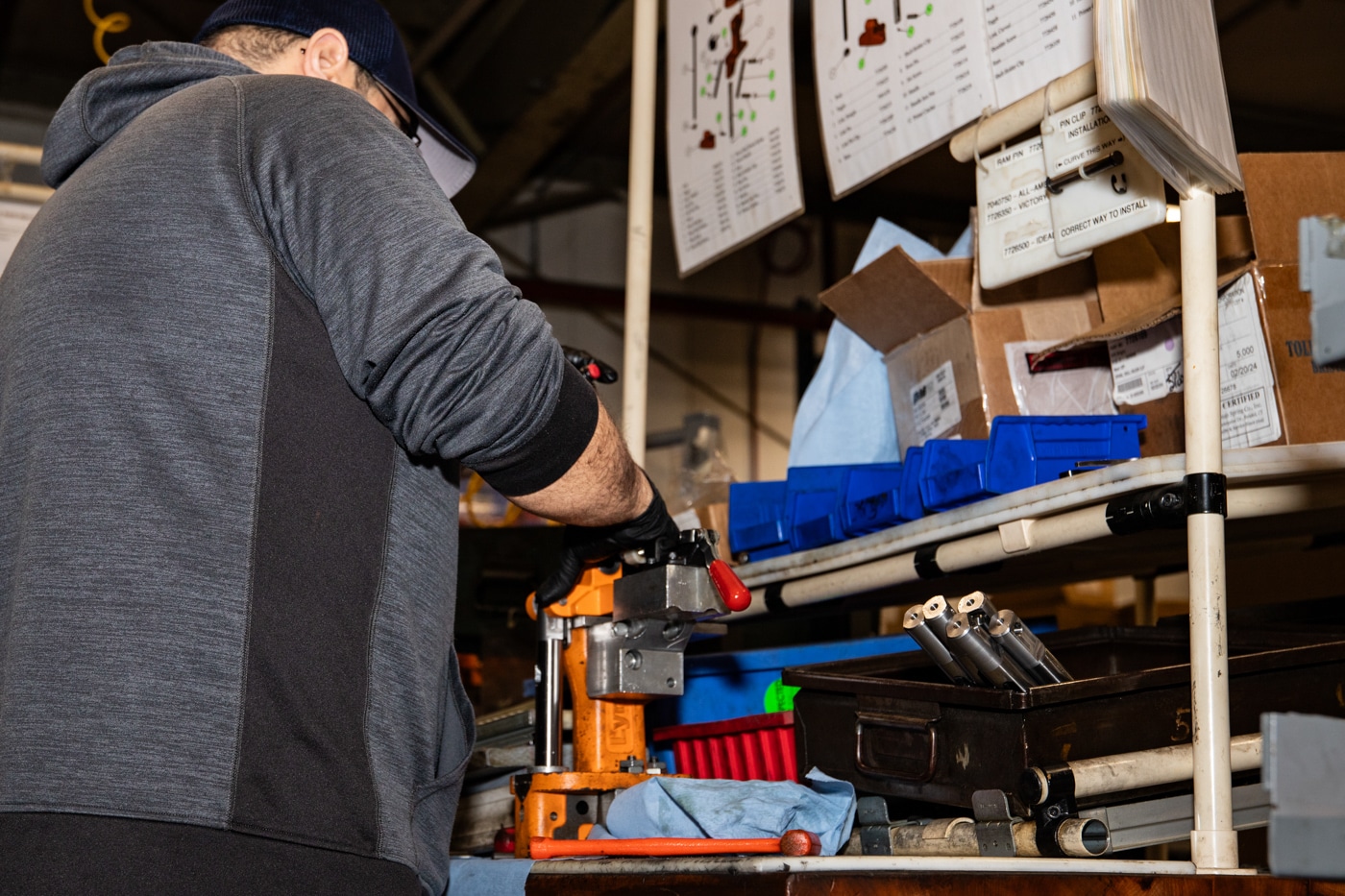
Manufacturing anything from raw materials produces metal shavings, and to be as efficient as possible Lyman sells the metal shavings to a scrap dealer. Another cost-control measure — begun 10 years ago — involves using a bar code system (Enterprise Resource Planning — ERP) to track all of the different dies that are produced. The computerized system knows where everything is at all times. This makes factory floor workers more efficient.
In 2019, Lyman purchased Mark 7 reloading — a company that manufactures automated reloading machines. Mark 7 machines bring progressive reloading to full automation.
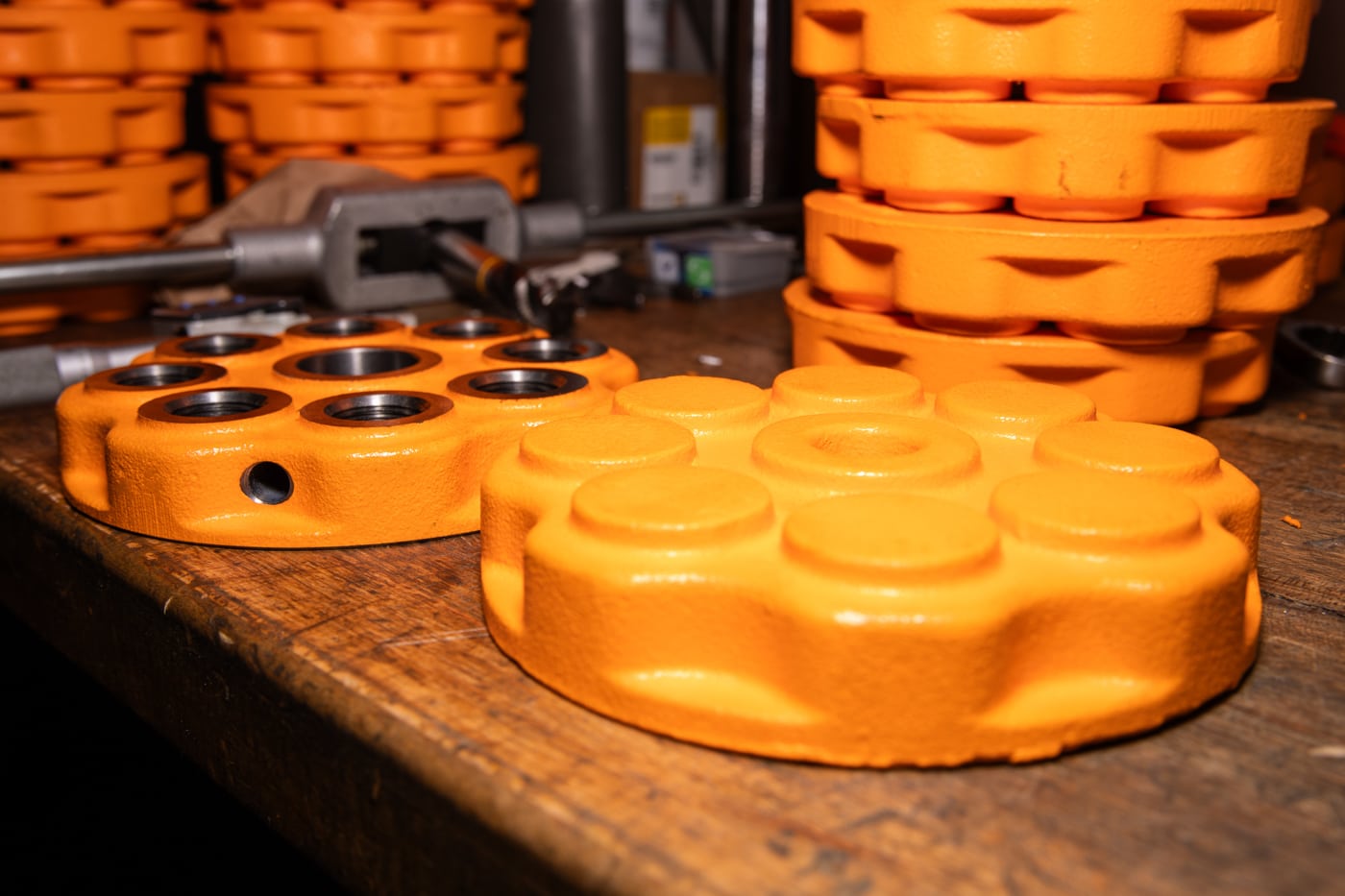
Mark 7 machines have ten stations and an autodrive. The machines are designed to run on their own to make ammunition in large quantities. The 10 stations separate every step: decapping and sizing are done separately as are flaring, powder dispensing and powder checking. Bullet seating and crimping are also separate functions. According to Lyman, station separation produces superior results.
Mark 7 machines are built for automated reloading, and are available in models designed for everything from individual manual use like the Apex 10 (which an autodrive can be added to later), all the way up to full commercial loading like the new Titan. Many commercial reloaders rely on Mark 7 machines. While the Mark 7 machines are built in Fort Myers, Florida, many of the parts are fabricated in the Middletown factory.

I know a home reloader — a high volume shooter — who uses two different Mark 7 presses: a Revolution and an Apex with automation. He told me that once the machine is properly set up and adjusted, the Apex can easily make about 2,500 9mm cartridges per hour. He said the learning curve is steep, but “the Mark 7 team in Florida has provided excellent customer support”. He told me: “my journey with Lyman reloading products has been nothing short of exceptional.”
Lyman designed the Stainless Steel Pro Dies to work with high-speed, high-volume, automated equipment — like their own Mark 7 machines. Pro Dies are made in Connecticut for 17 popular rifle and pistol calibers. These dies have a 7/8 X 14 thread pitch and can be used with any press.
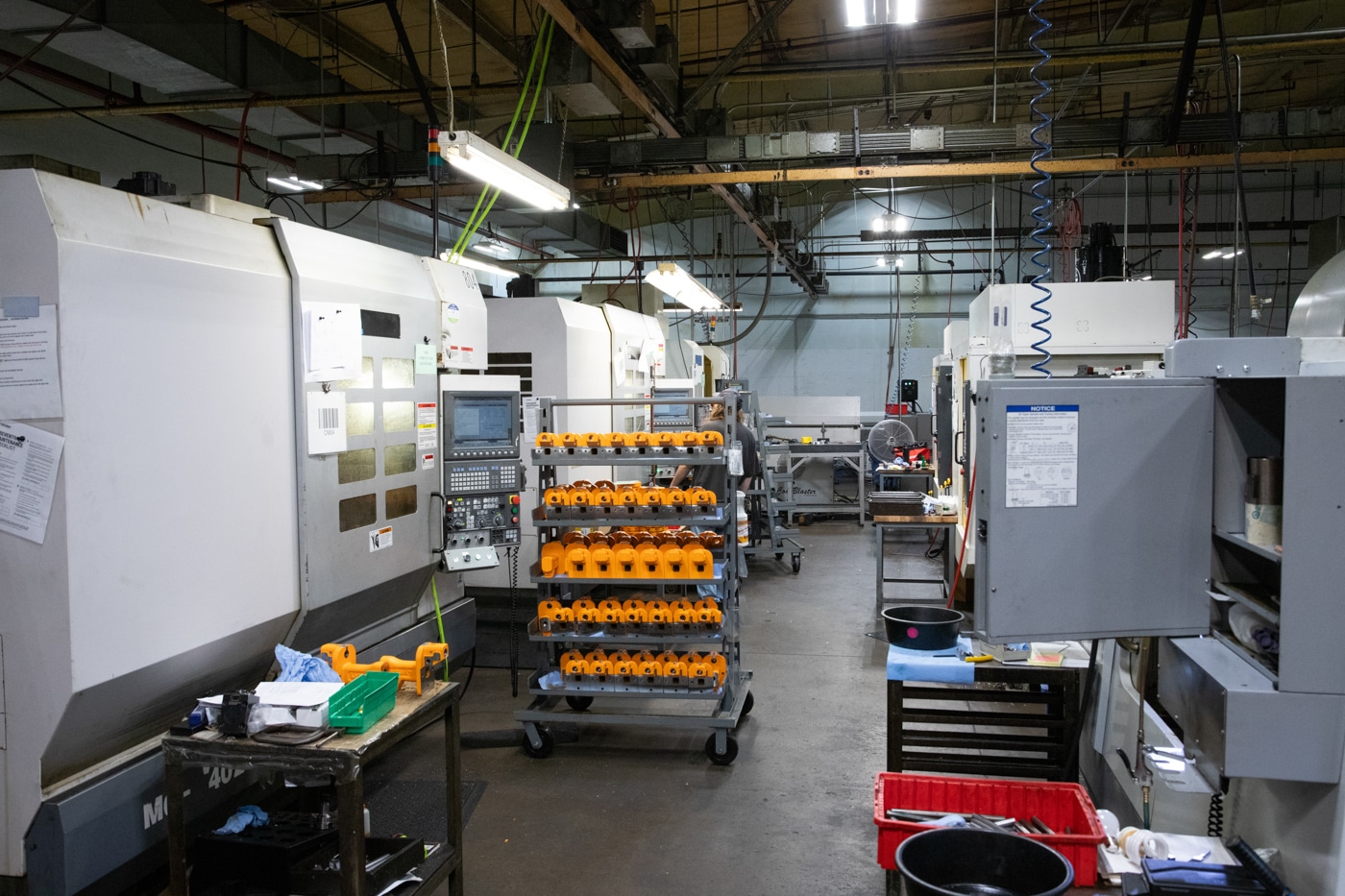
Others, like the Premium Carbide 4 Die Sets, are made for modern, popular calibers. Lyman also makes dozens of other dies such as, MSR die sets which are specific for AR calibers, popular rifle and pistol die sets, as well as specialty dies like the “M” Neck Expanding Die, the Universal Decapping Die and the Ram Prime Die.
Conclusion
I was fortunate to get to meet many Lyman employees, all of whom seemed to be genuinely happy in their jobs. A board showing the many employees who have several decades of service to the company underscores this. Plainly, Lyman treats its employees well; morale is high, and that results in high-quality products for shooters.
Today’s Lyman is a modern manufacturer of all things firearms. Anyone who is serious about firearms and shooting should consider Lyman products for their shooting, reloading and gun maintenance needs.
Editor’s Note: Please be sure to check out The Armory Life Forum, where you can comment about our daily articles, as well as just talk guns and gear. Click the “Go To Forum Thread” link below to jump in and discuss this article and much more!
Join the Discussion
Featured in this article
Read the full article here